The TLDR: Too busy to read? Here's a quick summary of article
Modern electronics are growing ever more complex—with systems now deeply interconnected—yet traditional safety analyses like FMEDA remain manual and outdated. This gap is stark when compared to the automation and continuous integration processes thriving in software development, highlighting an urgent need to modernize hardware safety methods.
In today’s ever-evolving world of electronics, more features mean more complexity. Systems are now more interconnected and interdependent than ever—just think of incidents like the CrowdStrike outage or the BMW recall due to an issue with the integrated braking system built by auto supplier Continental. A recent Modelwise survey found that analyzing an automotive control unit PCB with 300–500 parts can require between 1,000 and 5,000 individual assessments, each taking 10–30 minutes. That totals roughly 500 hours for the analysis and another 500 hours for documentation!
Traditional safety methodologies, like FMEDA (Failure Modes, Effects, and Diagnostic Analysis), have been a cornerstone of functional safety analysis for decades, even after being around for more than half a century. Yet, as systems become more complex, these methods are under immense strain due to increased intricacy, greater system connectedness, a scarcity of functional safety engineers, time-to-market pressures, and fragmented tool chains. Simply put, while FMEDA remains essential, the way we perform it today needs a radical rethink.
Taking a step back, it’s clear that while software development has long embraced automation and continuous improvement—automatic builds, testing pipelines, and iterative feedback loops—hardware development lags behind by a mile. The comforts of modern software development are not yet standard in hardware development.
The SCSC Context
At the 33rd annual Safety Critical Systems Symposium (SSS’25), held in York, UK in February 2025 and organized by the Safety Critical Systems Club (SCSC), the main themes centered around AI, complexity, and security—each critical to modern systems and each posing unique challenges in terms of safety assurance. With six keynote talks from distinguished experts and six technical workshops (including poster sessions), I also had the opportunity to present both a pitch and a poster at the symposium. My poster presentation, “Continuous FMEDA – from Circuit to System,” addresses the gap between software and hardware development, exploring how the traditional, one-off FMEDA process can evolve into a scalable, continuous analysis—from individual electronic circuits up to the system level.
“Continuous FMEDA” draws inspiration from the concept of “Continuous Integration” (CI) in software engineering. CI involves automatically building and testing every change to the software through an automated pipeline, ensuring that the software maintains correct functionality throughout the development process. How can we translate this concept to FMEDA?
The concept of “Continuous FMEDA” involves integrating the well-established FMEDA process into a continuous, iterative framework that aligns with modern development practices. Whenever there are changes to the electronic design or updates to safety requirements, FMEDA is automatically triggered to analyze the impact on system reliability and safety. This new paradigm provides live feedback to design and engineering teams, highlighting areas for improvement, which is only possible by automating FMEDA.
The good news is: automation of FMEDA for electronic circuits is state of the art. At Modelwise, we offer exactly that. Once configured, FMEDA can be embedded in automated workflows similar to CI pipelines in software engineering. Our advanced model-based algorithms automate the manual and cumbersome analysis—essentially serving as a “spell-checker” for electronic circuit designs.
The benefit of continuous FMEDA starting at the lowest level, is that it provides you the building blocks for systems and systems of systems. A Lego-like building process (ref. Component-fault-trees) enables system integration testing and verification of the safety architecture.
If this is something that excites you, or if you have feedback or suggestions, feel free to reach out to me on LinkedIn.
Key Takeaways from the Symposium
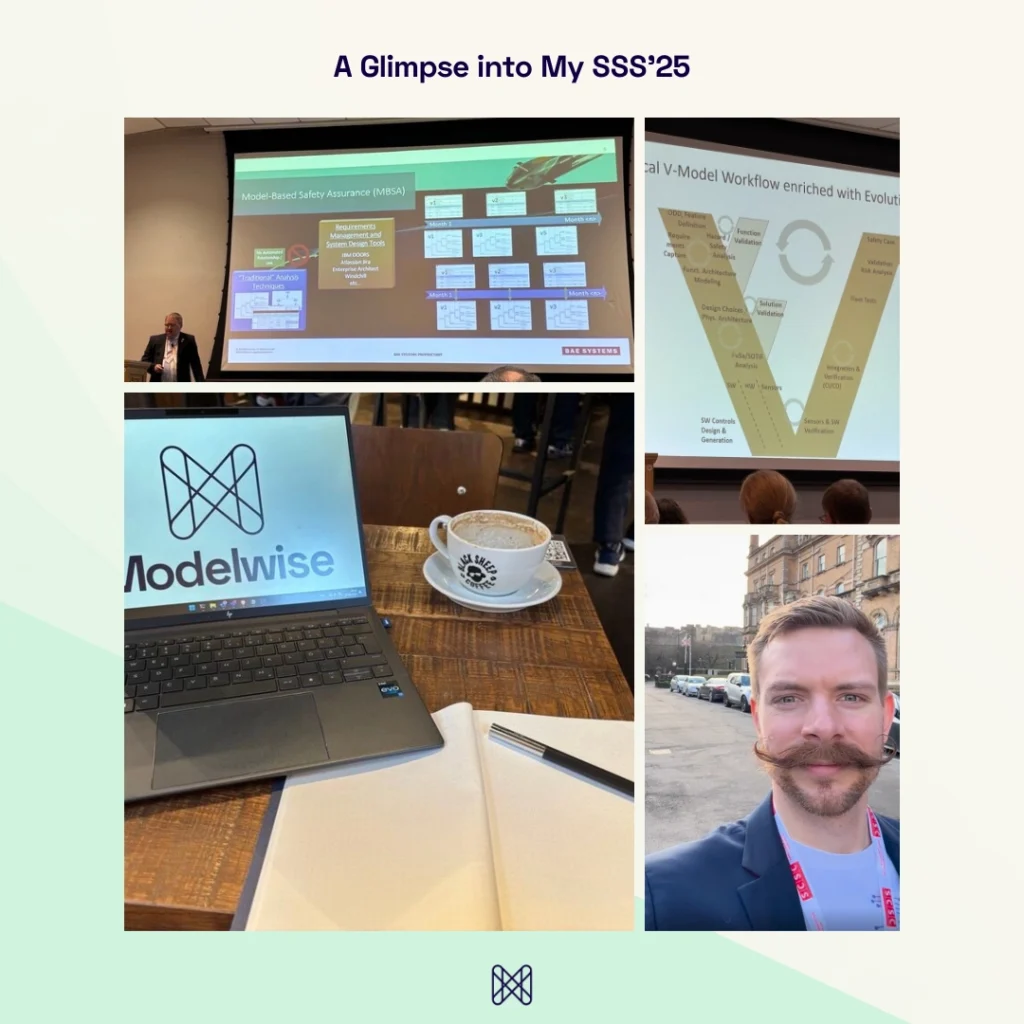
Rethinking “Safety-Critical”:
Dewi Daniels and Mike Parsons 1 opened the symposium with a powerful reflection on the Post Office scandal in the UK. His talk highlighted that even systems not traditionally deemed “safety-critical” can cause severe harm if they fail—challenging us to broaden our safety remit.
This sentiment is echoed by our customers – applying safety processes and analyses on traditionally non-critical systems can significantly enhance product reliability and resilience, a shift previously hindered by the substantial overhead of conventional safety methods.
Innovating Safety Analyses:
The debate on the role of AI in safety analyses was both lively and thought-provoking. While some advocated for the cautious use of generative AI in building safety cases, I remain a strong proponent of deterministic, model-based reasoning for automating processes like FMEDA. It’s all about ensuring our analyses remain rigorous and traceable.
Real-World Impact of MBSA:
Presentations by Kevin King and Rahul Nair 2 and Bernhard Kaiser et. al. 3 showcased how model-based approaches are already making a tangible impact. They shared insights into Model-Based Safety Assurance (MBSA) and the use of SysML V2 throughout the product lifecycle, reinforcing that agility in safety engineering is not just desirable—it’s essential.
The full proceedings of SSS’25 can be found here.
Looking Ahead
SSS’25 has left me with plenty to ponder. The challenges in modern safety engineering are significant, and the ideas exchanged during these sessions have paved the way for innovative approaches. At Modelwise, our commitment remains clear: to speed up hardware safety analysis and to elevate the quality of safety-critical development across all system designs.
Let’s continue the conversation on transforming safety in our increasingly complex world.
Comments, suggestions? Brickbats, bouquets? Please send your feedback to our editor.
Footnotes
Disclaimer: Some resources provided are behind a members-only or registration wall.
[1] Looking Beyond the Horizon
[2] The challenges of assuring an eXtra Large Autonomous Underwater Vehicle